Sobre la empresa
Empresa dedicada a la manufactura y desarrollo de tecnología de vanguardia para la industria automotriz.
Problemática inicial
Experimentaban falsos rechazos y contaminación de aceite en la línea de ensamble de cilindro maestro, donde se controla y distribuye el líquido de freno de llantas.
En esta parte del proceso utilizaban 2 bombas lubricadas mediante el aceite “CP3 Oil” (no corrosivo) para detectar posibles fugas en el depósito del líquido de frenos del automóvil.
Sin embargo este aceite se adelgazaba rápidamente por su composición especial y se filtraba, ocasionando contaminación por derrame en el área de trabajo y contaminación al interior del motor, liberándose como vapores en el ambiente.
Retos
- Aumento del 30% en los costos de refacciones de acuerdo al consumo estándar en este tipo de bombas.
- Se tenía que cambiar el retén aproximadamente cada 4 - 5 meses, cuando en realidad debía durar un aproximado de 10,000 horas (1 a 2 años dependiendo del proceso según el fabricante).
- Alto consumo de aceite con 1 - 2 L por semana, cuando de acuerdo al fabricante se recomienda cada 6 meses (este equipo tiene una capacidad de 2L).
- Falsos rechazos en la línea de producción debido a la pérdida de las propiedades del lubricante, el cual no cumplía su función de sellado para alcanzar el vacío requerido.
- Paros de línea una vez al mes, durante 1 hora por cada bomba para realizar el cambio de lubricante y piezas dañadas.
- Aumento en las horas/hombre de mantenimiento.
- Incremento en la compra de kits de mantenimiento debido al corto de tiempo de vida de las piezas.
- Derrames o emisiones de aceite con impacto ambiental negativo.
- Los vapores emitidos ocasionaban irritación al ser inhalados, afectando la salud del trabajador.
Nuestra solución
Se analizó la implementación de un equipo libre de aceite para eliminar de raíz el problema generado por el lubricante. También se encontró la opción de colocar un equipo de mayor capacidad que permitiera reducir el número de equipos en la línea, mejorando el consumo energético y layout.
La versatilidad de la bomba con tecnología seca VaroDry VD 65 permitió que la instalación fuera “plug & play” reduciendo los tiempos de paro de línea para la adaptación del sistema.
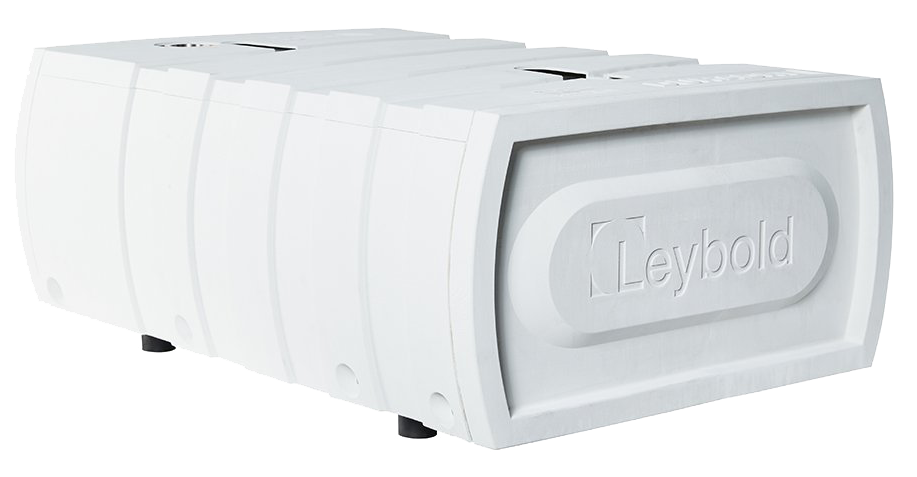
Beneficios obtenidos
- Se eliminó la contaminación en la línea de producción.
- Sin consumo de kits o aceite.
- Libres de mantenimiento
- Eliminación total de los paros de producción
- Reducción del 30% aprox en el consumo energético al usar un solo motor.
- Protección de la salud del personal al eliminar los vapores de aceite.
- Se eliminaron los residuos de aceite de la bomba de vacío.
- Sin riesgo de derrames ni gases contaminantes para el medio ambiente.